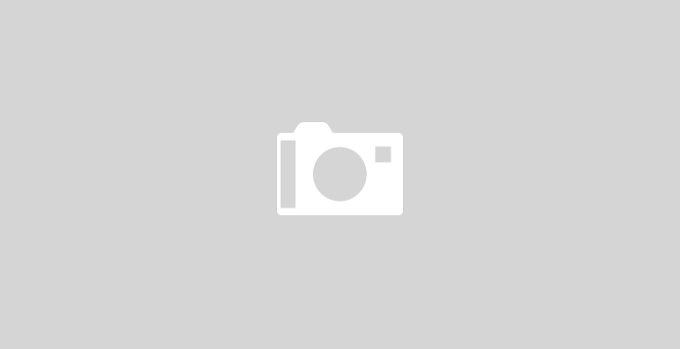
Timing
Timing closure impacted by DVFS!!
While designing systems with DVFS techniques, we need to look at the impact of temperature inversion on the performance…
While designing systems with DVFS techniques, we need to look at the impact of temperature inversion on the performance…
There are various voltage scaling approaches that are in use today, Static Voltage Scaling: Different blocks in t…