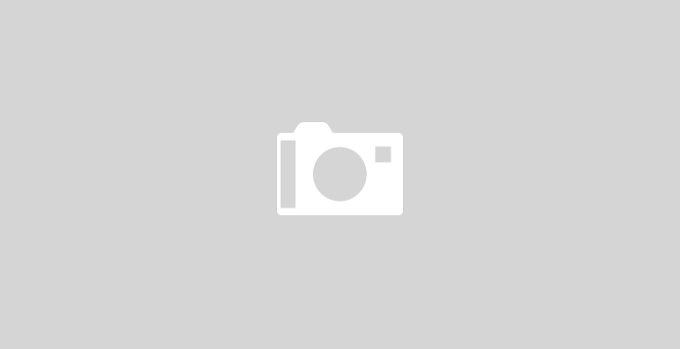
Interview Question on Power Analysis
Your task is to do power analysis for a circuit that sends out a one-clock-cycle pulse on the done signal once every 16…
Your task is to do power analysis for a circuit that sends out a one-clock-cycle pulse on the done signal once every 16…
Power gating adds enabling signals to a power supply network; dynamic power supply management adjusts supply voltage ac…
This paper , using an example design, demonstrates how to meet challenging performance, latency and bandwidth goals by …
Displays have always been a major power consumer in mobile devices. In the past, one easy way to keep power demands in …
Systems designers are having a difficult time developing power subsystems that supply all of their system's power n…
EETimes has published an article on the Top 10 Power Management articles of 2008. {Follow Here}
A scalable approach to chip architecture is essential and valuable since a SOC design today often becomes a component i…
A good working definition of architecture ( in the context of IP design, atleast) is the partitioning and interface des…
How can we retain state of some of the registers in the design? How to deal with memory state? Let me try to explain…
While designing systems with DVFS techniques, we need to look at the impact of temperature inversion on the performance…
There are various voltage scaling approaches that are in use today, Static Voltage Scaling: Different blocks in t…
Due to a miscommunication during design, you thought your circuit was supposed to have a supply voltage of 2.1 volts (t…
This article is about RTL in a Multi-Voltage environment and it's implication on verification. In the earlier …
Lets take a look at the various low power techniques in use today. I would classify them into 2 categories Structu…
Special cells are required for implementing a Multi-Voltage design. Level Shifter Isolation Cell Enable Level Shifter…
Before we start looking at implementing a Multi-Voltage design there are certain questions that need to be answered to …
In the last few weeks i have been quite busy with a lot of research on low power design. There are so many tutorial…
Multi-Vt placement/spacing concerns I was just thinking about most common concerns faced today in addressing leakage p…
Primarily design for low power depends on the characteristics design being accomplished. If it is a multi-million gate …