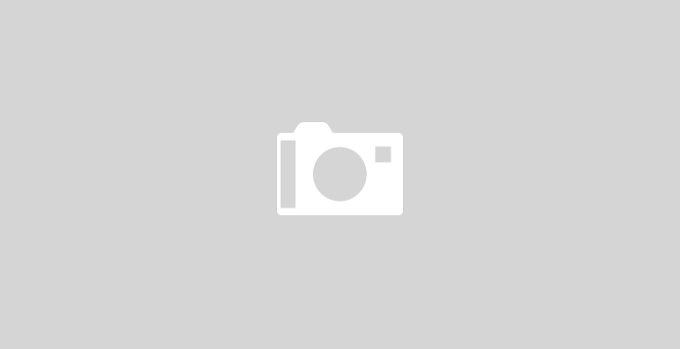
Investigation on timing analysis inaccuracies
Timing analysis inaccuracies due to crosstalk, multiple gate input switching, supply voltage variation, temperature, ma…
Timing analysis inaccuracies due to crosstalk, multiple gate input switching, supply voltage variation, temperature, ma…
How do you quantify the effect of WireLength Models (WLM) and target frequency on the post-routing timing results?
Q1: How would you speed up an ASIC design project by parallel computing? Which design stages can be distributed for pa…
Sometimes the delay through a component is dependent upon the values on signals. This is because different paths in the…
Because of shrinking feature sizes and the decreasing faithfulness of the manufacturing process to design features, pro…
This Mentor's Verification Academy module directly addresses CDC issues by introducing a set of steps for advancing…
Functional simulation : Simulation of a design description. This is also called spec simulation or concept simulation. …