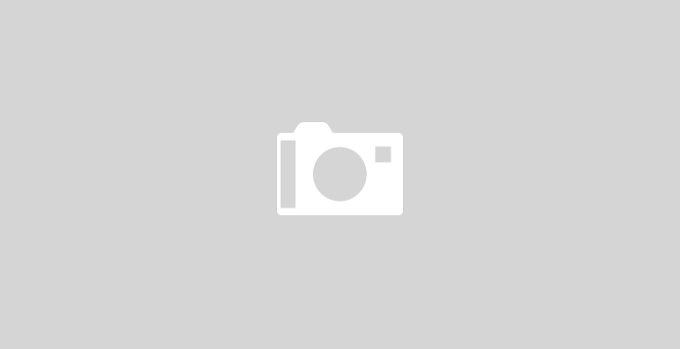
Low Power
Infrastructure Needs for Multi-Voltage Designs
Before we start looking at implementing a Multi-Voltage design there are certain questions that need to be answered to …
Before we start looking at implementing a Multi-Voltage design there are certain questions that need to be answered to …
In the last few weeks i have been quite busy with a lot of research on low power design. There are so many tutorial…
Multi-Vt placement/spacing concerns I was just thinking about most common concerns faced today in addressing leakage p…